History
Onamac Industries commenced business in 1974.
In 2016 Onamac expanded into a new 60,000 square foot, state-of-the-art, climate-controlled facility located 1 mile north of Boeing's Paine Field. Onamac employs over 125 Manufacturing and Quality Engineers, Machinists, Assemblers, and Administrative Support.
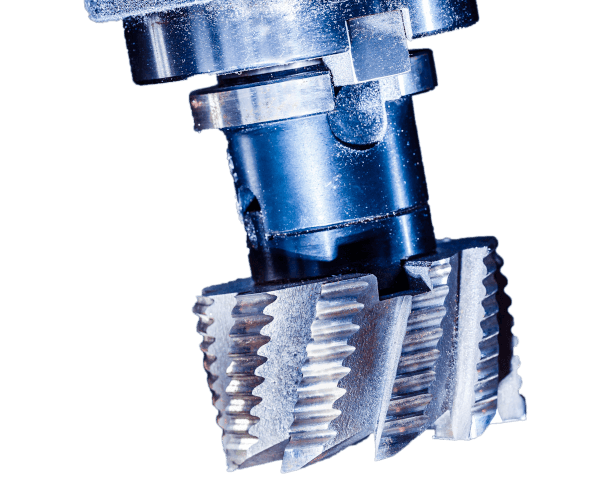
Mission statement
Onamac is a world-class manufacturer of multi-axis milled, turned, and assembled aerospace components, specializing in the machining of investment castings.
Our vision
Onamac's vision is to continually strive to be an employer of choice in our community and a supplier of choice in our industry.
Award-winning Supplier
Over the past 20 years, Onamac has won numerous customer awards. Notable among these awards is the 2014 Boeing Supplier of the Year, 2017 KHI Supplier of the Year, and 2022 KHI Supplier of the Year, as well as several Boeing Performance Excellence awards.
Onamac has developed strong working relationships with their customers, founded on the quality and timeliness of the Company's output.
The perennial recognition demonstrates Onamac's commitment to going beyond the technical requirements to solve unforeseen issues, respond to last minute requests, and make suggestions to improve quality and decrease costs.
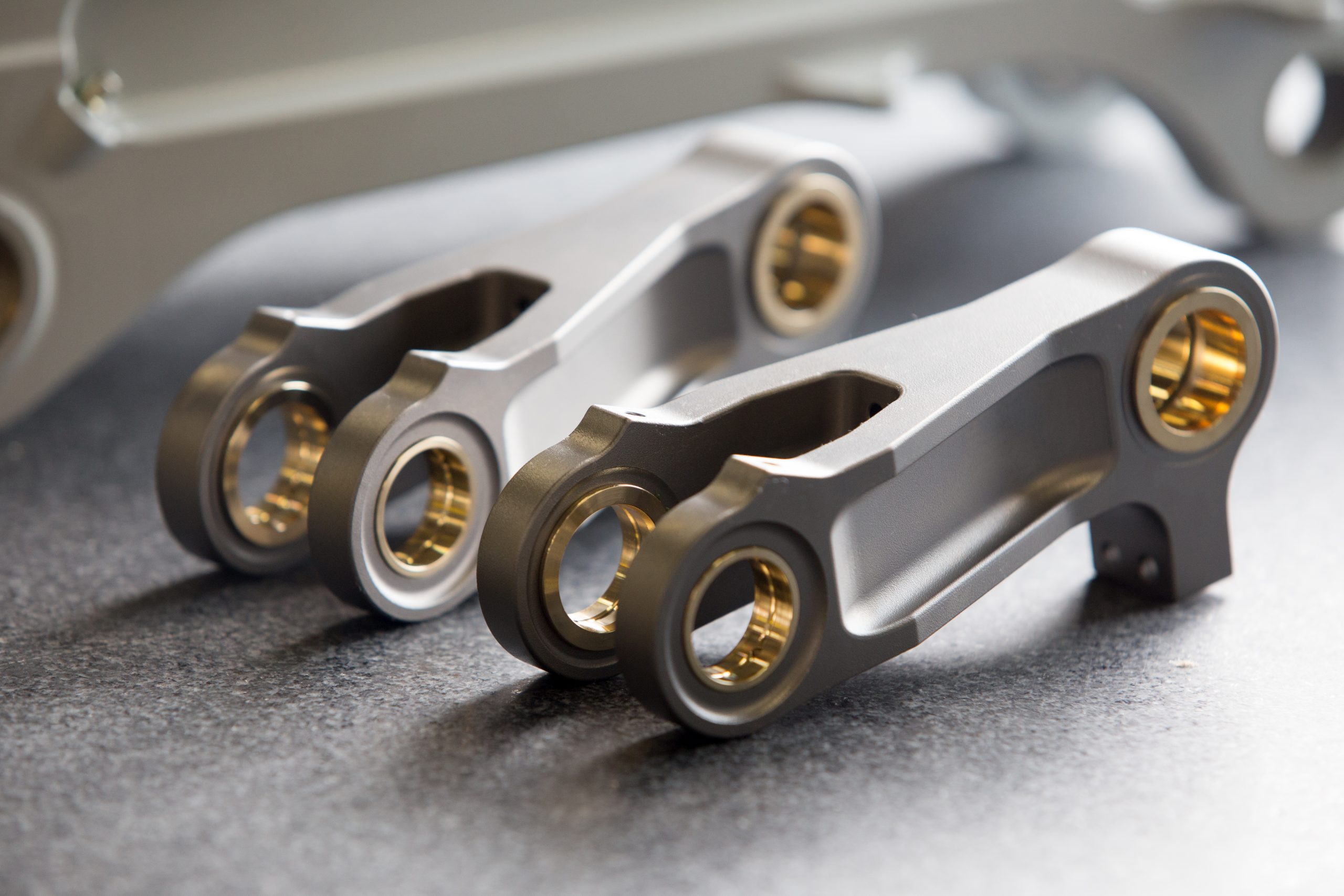
Capabilities
Onamac has over 40 production machines to produce tight tolerance milled and turn parts for the Aerospace industry. Onamac has recently expanded its capabilities to machining Titanium castings to support the jet engine aerospace market.
Our services include:
- CAD/CAM Engineering and Drafting
- CNC Simultaneous turning and milling 7 Axis
- CNC Milling 3-4-5 Axis
- CNC Lathe Operations
- Conventional Machining
- OD Grinding
- Hardware Insertion
- Mechanical Finishing & Assembly
Quality inspection capabilities
- AS9100 Rev D 2016 Certified
- ISO 9001 2015 Certified
- Climate Controlled Quality Laboratory
- Calibration system traceable to NIST
- Coordinate Measuring Machine
- 30" X 24" X 18" Capacity
- Part Tracing and Surfacing
- CAD Interface with IGES Translation
- Air Gage system with Resolution to .00005"
- Optical Comparator with Surface Reflection
- Surface Finish Analyzing Equipment
- Comprehensive Specification Library Including
- Military, MS, AN, ASME, and ASTM Standards
- Airbus Certified, 01 Joining Tech.
- Heroux Devtek, HPS-210 Assembly
1974
Company founded in Camano Island, WA
1988
Onamac becomes Boeing-approved source
1994
Awarded with first Spares Commodity Contract from Boeing for 400 bushings
1996
Moved to new facility near Paine Field, Everett, WA
1999
Boeing Commercial Supplier of the Year Award
2000
Boeing's President's Award for Excellence
2003
Boeing Enterprise Supplier of the Year
2007
Began 787 and P8A Poseidon production work for Tier 1 production companies
2008
First Boeing POP LTA signed, Extension of Boeing Spares LTA finalization, major award of Boeing Spares Large Milled Parts
2010
Boeing 787 Ground Support Contract
2010 - 2012
Boeing Performance Excellence Award
2013
Boeing Performance Excellence Award
2014
Boeing Supplier of the Year
2016
Moved to new facility near Boeing, Merrill Creek
2017
Kawasaki Heavy Industries Supplier of the Year
2022
Kawasaki Heavy Industries Supplier of the Year
Materials Expertise
Onamac has experience machining a wide variety of metals with aerospace applications. Depending on the design and end purpose of the required part, there are several alloys and machining methods that can be used to arrive at the required confluence of strength, flexibility, weight, durability, and economics. The influence of these factors changes for each part of the aircraft.
Metals Machined | Characteristics | Example Aerospace Application |
---|---|---|
Aluminum | Soft metal, light & durable | Wing leading edge, landing gear components & support fittings, and floorbeams |
Aluminum-Nickel-Bronze | Soft metal, highly resistant to corrosion | Bearings, landing gear components |
Inconel | Hard metal, used in high-temperature applications | Engine parts |
Stainless Steel (13-8, 15-5) & Steel Alloys (300M, 4330, 4340) | Hard metal, highly resistant to corrosion | Structural components |
Titanium | Hard metal, extremely high strength-to-weight ratio | Engine & frame components |
Machine List
close
Major Aerospace Customers
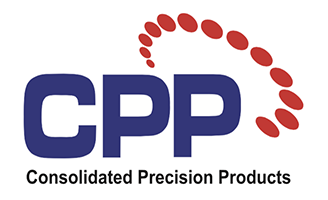
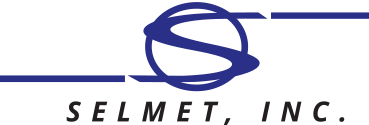
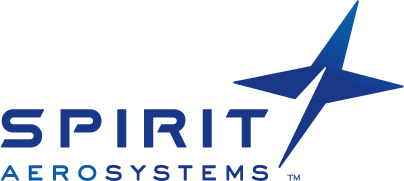
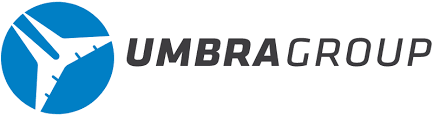
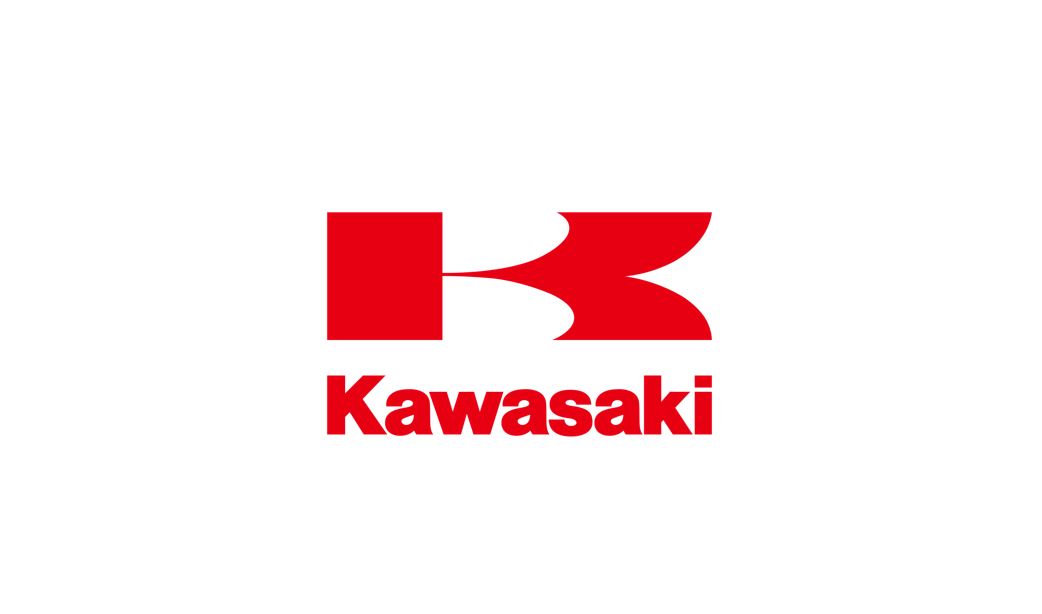

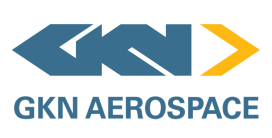
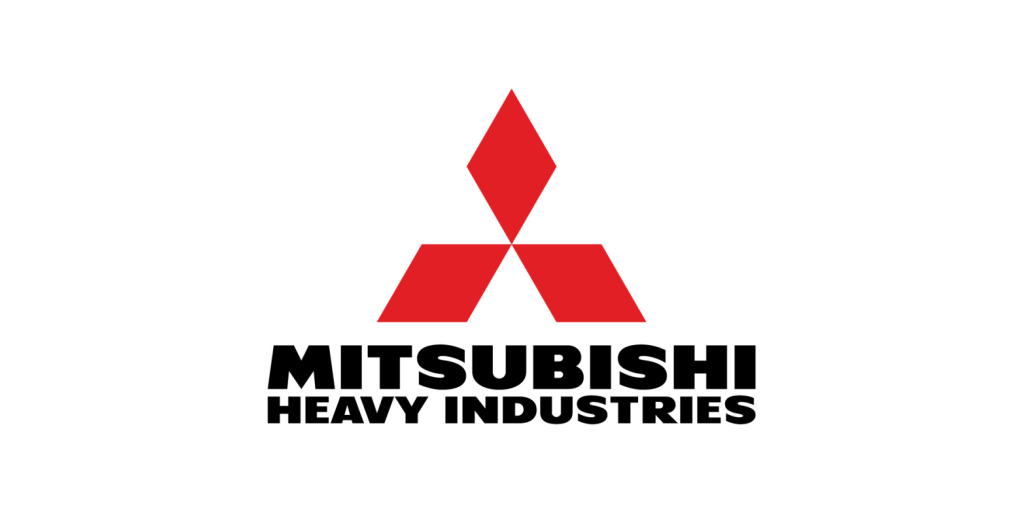

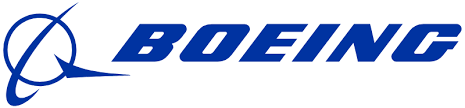
